News Story
McGregor: Harnessing the Potential of Additive Manufacturing
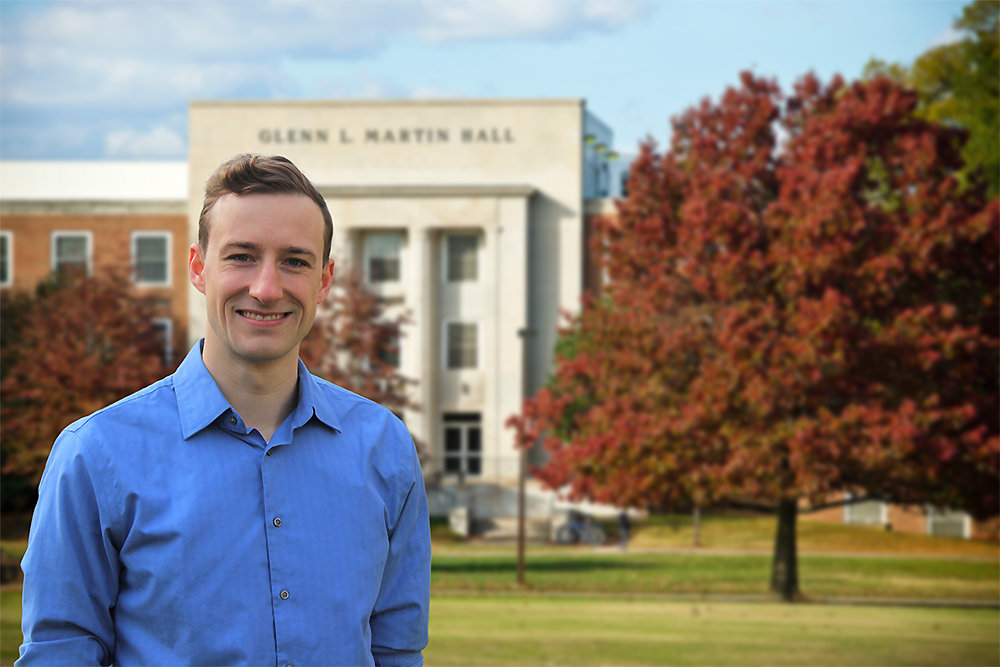
Additive manufacturing, which entails designing an object in a software program and then fabricating it layer by layer, has long been used for prototyping. But the emergence of high-accuracy 3D printers and engineering materials has prompted increased use of such techniques to create end-use components and products.
Davis McGregor, the newest member of the mechanical engineering faculty at the University of Maryland’s (UMD) A. James Clark School of Engineering and a Fellow at the Fischell Institute for Biomedical Devices, sees a variety of industries embracing the technology.
"The top safety-rated helmets used in the NFL today are produced using additive manufacturing—the traditional foam inside the helmets is replaced with 3D printed lattices," he said. “Shoes, medical devices, and many more end-use parts are also being 3D printed for customizable, and often improved, performance."
"We’ve been able to 3D print critical aerospace components with metal printers for close to 10 years now," he said, "although the number of flight certified parts remains small."
The lag in aerospace is partly due to the need to ensure greater reliability, McGregor said. Conventionally manufactured components often have different qualification processes than additive ones, relying on extensive historical manufacturing knowledge aggregated over centuries.
Similar components produced using additive manufacturing typically require rigorous inspection–a time-consuming and expensive process that has hindered adoption. Research being conducted at McGregor’s’ MIRAGE (Manufacturing Intelligence Research and Advanced Geometry Evaluation) Lab could help close that gap.
"The top safety-rated helmets used in the NFL today are produced using additive manufacturing—the traditional foam inside the helmets is replaced with 3D printed lattices. Shoes, medical devices, and many more end-use parts are also being 3D printed for customizable, and often improved, performance. We’ve been able to 3D print critical aerospace components with metal printers for close to 10 years now, although the number of flight certified parts remains small."
Davis McGregor, Assistant Professor of Mechanical Engineering and Fellow, Fischell Institute for Biomedical Devices
At MIRAGE, he and his team are investigating two research areas that are crucial to the wider adoption of additive manufacturing: advanced metrology and manufacturing intelligence.
Metrology, the science of measurement, allows engineers to assess whether a 3D-printed part or component will perform as intended. The team leverages computer vision and other software tools to automatically inspect part quality and identify manufacturing defects.
Manufacturing intelligence brings AI and machine learning into the process, harnessing data to understand and improve part quality.
Together, these approaches can help engineers ensure that additively manufactured parts, whatever the applications may be, are reliable and safe.
McGregor, who joined the UMD faculty in Fall 2023, has been on both sides of the academia-industry relationship: after earning his PhD. from the University of Illinois Urbana-Champaign in 2022, he went to work in the private sector. Having now transitioned to an academic career, he brings with him an understanding of specific industry needs.
UMD was an attractive choice for McGregor because of its many opportunities for cross-disciplinary collaboration. For instance, McGregor has an interest in additive manufacturing for biomedical applications, including surgical guides, implants, and patient-specific parts.
McGregor's appointment as a Fischell Fellow, and UMD’s ongoing partnerships with the University of Maryland Medical School (UMMS), provide opportunities to develop those interests. “The research partnerships and resources at UMD are fantastic and pose many exciting possibilities for my work,” McGregor said.
Published June 10, 2024